The Evolution of Molding Plastics in the Metal Fabrication Industry
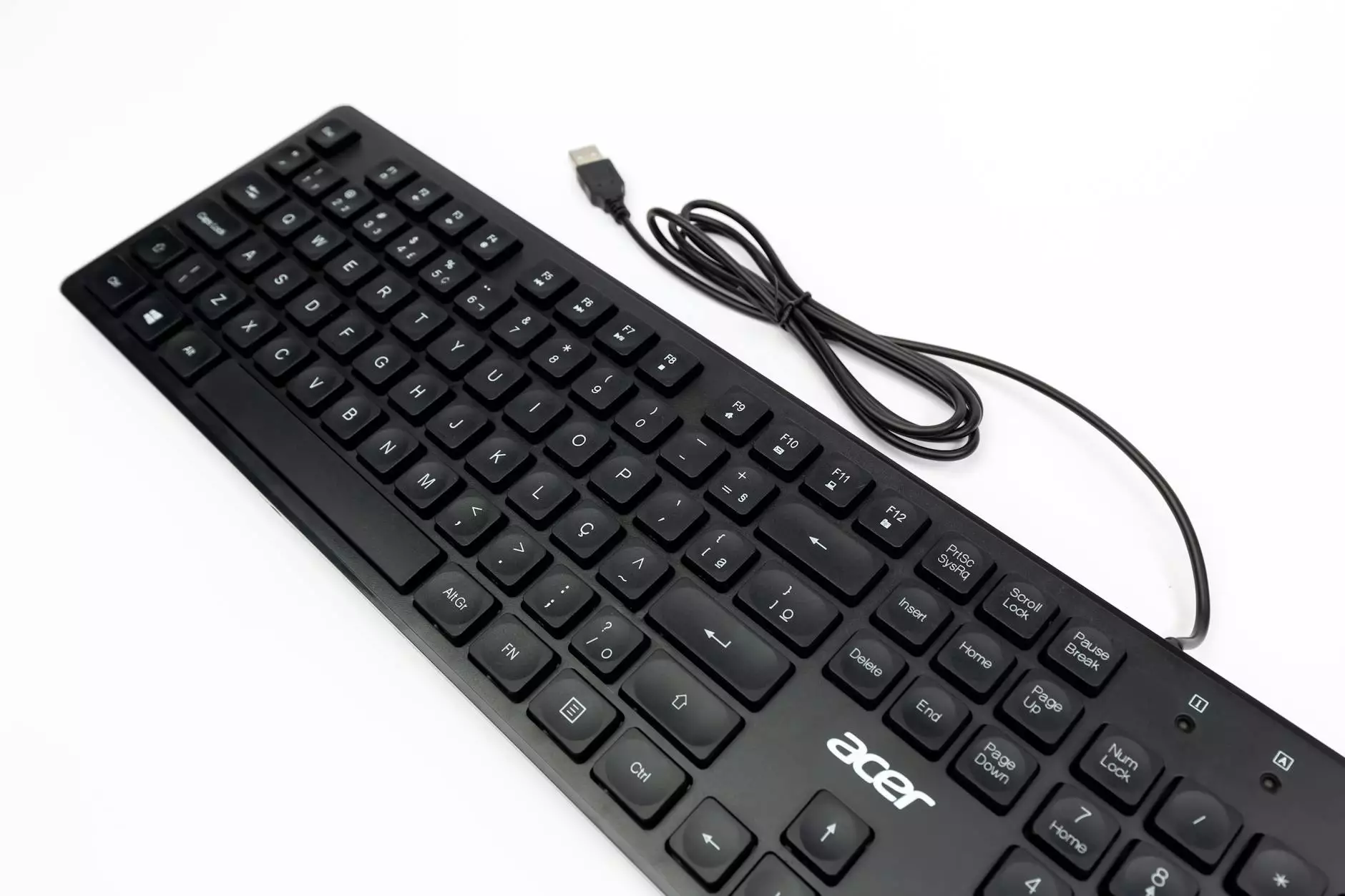
Molding plastics has revolutionized the manufacturing landscape, allowing companies to produce complex and high-quality components with unparalleled efficiency. For businesses in the metal fabrication sector, understanding and integrating molding plastics can lead to significant advancements in production capabilities and product quality. In this article, we will explore the various aspects of molding plastics, its benefits, and its implications for the future of industry within the realm of metal fabrication.
Understanding Molding Plastics
Molding plastics refers to a manufacturing process that involves shaping pliable materials into specific forms using molds. This technique is widely used across numerous industries, including automotive, consumer goods, electronics, and of course, metal fabrication. The process not only allows for the creation of intricate designs but also ensures that production can be scaled quickly and efficiently.
Types of Molding Plastics Techniques
There are several primary methods of molding plastics, each suited for different applications and material types. Here, we will highlight the most commonly used techniques:
- Injection Molding: This widely used technique involves injecting molten plastic into a mold to create precise, high-volume parts. Its advantages include minimal waste and rapid production rates.
- Blow Molding: Used primarily for hollow objects, blow molding involves inflating a heated plastic tube into a mold. This is commonly utilized in manufacturing bottles and containers.
- Rotational Molding: Ideal for creating large, hollow items, this method allows for even material distribution and is great for producing tanks and outdoor furniture.
- Thermoforming: This process involves heating a plastic sheet until it's pliable and then forming it over a mold. It's often used for packaging, trays, and automotive parts.
- Compression Molding: Primarily used for thermosetting plastics, this process compresses heated plastic into a mold. It's ideal for making durable parts including electrical insulators and appliance housings.
The Role of Molding Plastics in Metal Fabrication
Metal fabricators can significantly benefit from incorporating molding plastics into their operations. Here are some critical ways that this integration can provide value:
1. Enhanced Design Flexibility
One of the standout advantages of molding plastics is the design flexibility it affords manufacturers. With the ability to create complex shapes that would be cumbersome or expensive to achieve through traditional metal forming techniques, metal fabricators can push the boundaries of their product design and innovation.
2. Weight Reduction
Using molded plastic components in conjunction with metal parts can lead to significant weight savings without compromising strength. This is particularly important in sectors such as automotive and aerospace, where reducing weight can translate to better fuel efficiency and lower operational costs.
3. Cost Efficiency
By integrating molding plastics, metal fabricators can reduce material and production costs. Plastic components often require less energy to produce than equivalent metal parts, especially for high-volume manufacturing. Additionally, utilizing molding plastics can decrease the need for secondary operations like machining, further saving on costs.
Key Benefits of Molding Plastics in Metal Fabrication
The implementation of molding plastics within metal fabrication processes brings several notable benefits:
- Increased Production Speed: Molding plastics can be produced more quickly than traditional metal parts, allowing manufacturers to meet market demands with quicker turnaround times.
- Improved Durability: Plastics can be engineered to enhance their resistance to chemicals, UV light, and other environmental factors, extending product life and reducing maintenance costs.
- Customization: With advanced molding techniques, manufacturers can easily customize parts to meet specific client needs, increasing customer satisfaction.
- Eco-Friendliness: Many plastics used in molding are recyclable, leading to less waste and a smaller environmental footprint, which is increasingly important for modern consumers.
Challenges in Using Molding Plastics
While the advantages of molding plastics are significant, there are challenges that metal fabricators must navigate:
1. Material Limitations
Not all plastics offer the same strength characteristics as metals, which can limit their applicability in certain high-stress environments. Understanding the right materials to use in conjunction with metals is crucial for design integrity.
2. Quality Control
Ensuring consistent quality in molded plastic parts requires rigorous testing and quality control processes. Manufacturers must invest in these measures to prevent defects that can affect overall product performance.
Future Trends in Molding Plastics and Metal Fabrication
The future of molding plastics within metal fabrication looks promising, with several emerging trends that could further impact the industry:
1. Advances in Material Science
As material sciences advance, more robust and versatile plastics are being developed, opening up new possibilities for their application alongside metals. Composite materials that combine metal and plastic properties will likely become common.
2. Automation and Technology Integration
Automation in the molding process, such as the use of robotics for handling and assembly, will streamline production and enhance efficiency. Coupled with technologies like 3D printing, businesses can expect significant improvements in production capabilities.
3. Sustainable Practices
The push towards sustainability is encouraging the development and adoption of biodegradable and recycled plastics. Metal fabricators will need to adapt to these trends to meet consumer demands and regulatory requirements.
Implementing Molding Plastics at Deep Mould
At Deep Mould, the integration of molding plastics into our metal fabricating offerings exemplifies our commitment to innovation and quality. Our team continually explores cutting-edge technologies and techniques to ensure that we remain at the forefront of the industry.
Expert Consultation and Custom Solutions
We provide expert consultations to help businesses identify the best applications for molding plastics within their operations. Our tailored solutions not only enhance product innovation but also align with our clients' sustainability objectives.
Case Studies of Successful Implementations
Through collaborations with clients across various industries, we have successfully integrated molding plastics into diverse projects, showcasing our capability to adapt and thrive in an evolving market.
Conclusion
The synergy between molding plastics and metal fabrication is paving the way for a transformative era in manufacturing. Companies that embrace this integration can expect enhanced efficiency, product innovation, and competitive advantages in their respective markets.
For businesses looking to explore the potential of molding plastics, Deep Mould is your partner in navigating this exciting landscape. By understanding the intricacies of these manufacturing processes, we can help you thrive in an increasingly complex marketplace.