The World of Plastic Injection Mould Making
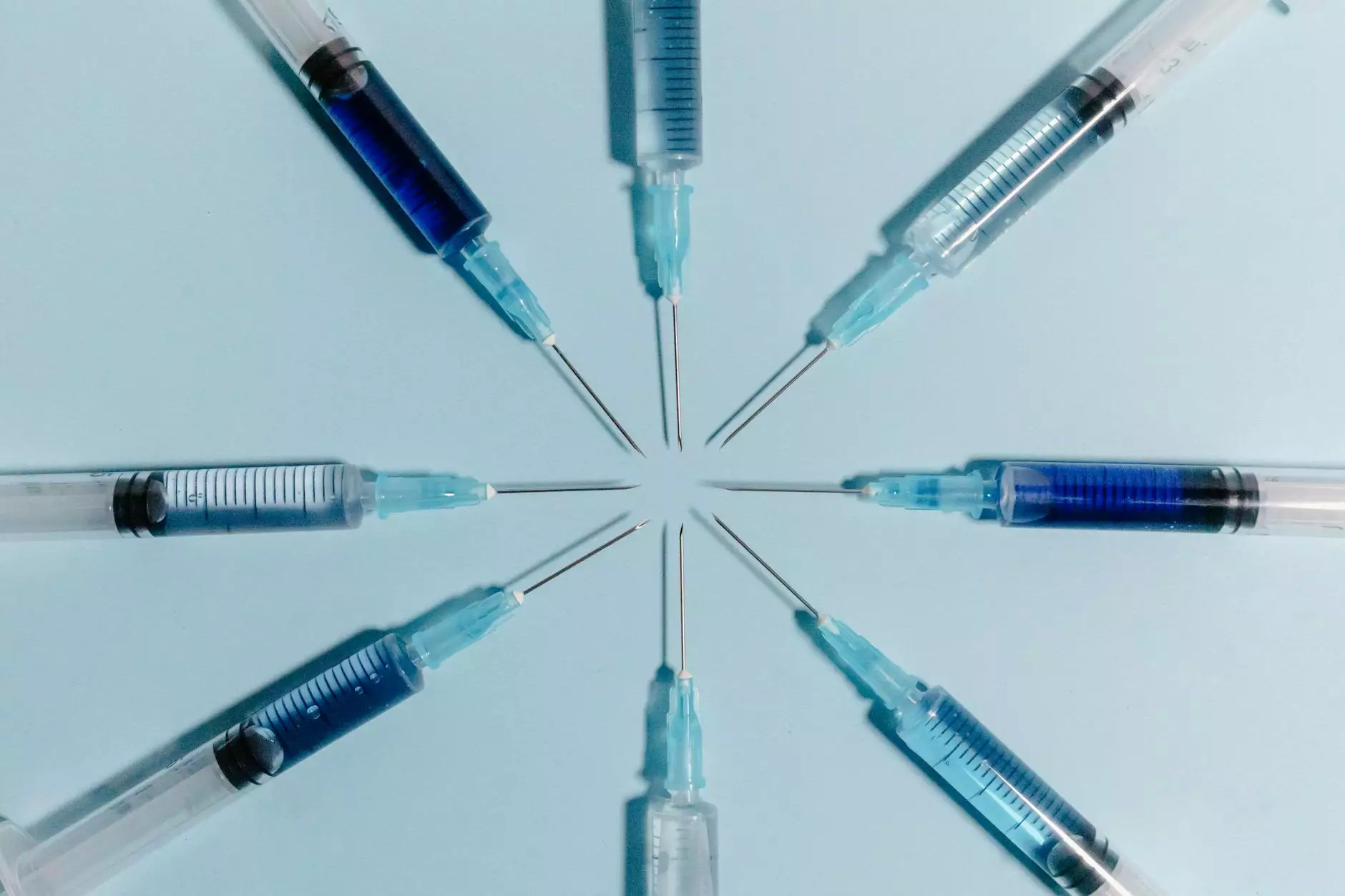
In the dynamic landscape of manufacturing, plastic injection mould making stands out as a critical process that speaks to efficiency, precision, and innovation. As one of the most versatile methods of producing plastic components, this process is foundational to countless industries, ranging from automotive to consumer goods. Here, we will explore the intricacies of this business, its significance, and what makes a leading plastic injection mould manufacturer like Hanking Mould a key player in this domain.
Understanding Plastic Injection Moulding
Plastic injection moulding is a manufacturing process where plastic material is melted and injected into a mould cavity, where it cools and solidifies into the desired shape. This method is highly favored in the production of large quantities of identical items due to its efficiency and accuracy. Here are some fundamental aspects of plastic injection moulding:
- Versatility: Suitable for various plastics, enabling production of diverse components.
- Cost-Effective: Ideal for mass production, reducing per-unit costs substantially.
- High Precision: Provides excellent dimensional control and surface finish.
- Speed: High production speeds capable of manufacturing large volumes in short timeframes.
Key Components of Plastic Injection Mould Making
The Injection Mould
The injection mould is the heart of the injection moulding process. It typically consists of two halves: the cavity and the core. The cavity is the part that forms the outside surface of the product, while the core shapes the internal features. Precision engineering during the design and fabrication of these components is crucial, as they directly impact the quality of the final product. Key attributes of an effective injection mould include:
- Durability: Moulds must withstand the high pressure and temperature of the injection process.
- Design Complexity: Ability to create intricate shapes not feasible with other manufacturing techniques.
- Ease of Maintenance: Designed for convenient upkeep to minimize downtime during production.
Materials Used in Injection Moulding
A wide array of materials can be utilized in injection moulding, which significantly impacts the properties of the final product. Common materials include:
- Thermoplastics: Such as polyethylene (PE), polypropylene (PP), and polystyrene (PS), known for their ability to be remolded.
- Thermosetting Plastics: Like epoxy and phenolic resins, which harden irreversibly and are used for more heat-resistant applications.
- Elastomers: Highly flexible materials used for products that require stretchability.
The Process of Plastic Injection Mould Making
The process of plastic injection mould making involves several critical stages, each requiring careful execution:
1. Design
Every successful plastic injection mould project starts with a detailed design. This step often includes:
- 3D Modelling: Utilization of software such as CAD to create precise digital representations of the product.
- Prototyping: Rapid prototyping techniques (like 3D printing) may be employed to validate the design before mould production.
2. Mould Fabrication
Once the design is finalized, the actual fabrication of the mould begins. This can involve the following:
- Material Selection: Choosing the right steel or aluminum alloy for mould construction, impacting durability and heat conduction.
- CNC Machining: High precision machining techniques to form the mould components, ensuring that they fit together perfectly.
3. Injection Moulding Process
During production, the process generally unfolds as follows:
- Melting: Plastic pellets are fed into an injection unit, where they are heated until they melt.
- Injection: The molten plastic is injected into the mould under high pressure.
- Cooling: The plastic cools down and solidifies within the mould.
- Demoulding: The finished part is ejected from the mould.
Benefits of Partnering with a Professional Plastic Injection Mould Maker
Choosing the right plastic injection mould maker is essential for delivering high-quality products consistently. Here are some key advantages:
- Expertise: Professional mould makers bring extensive experience and knowledge, providing insights from conception to completion.
- Quality Assurance: They adhere to stringent quality control measures, ensuring that each mould meets industry standards.
- Customized Solutions: Capable of creating custom mould designs tailored to specific client needs.
- Support and Maintenance: Providing ongoing support to troubleshoot and maintain mould functionality post-production.
Applications of Plastic Injection Moulding
The applications of plastic injection moulding are immense and span across various sectors. Here are some notable industries that heavily rely on this manufacturing technique:
1. Automotive
Modern automobiles consist of numerous plastic parts, from interior components to bumpers, all produced via injection moulding.
2. Consumer Electronics
Devices such as smartphones, laptops, and televisions utilize injection moulded components for durability and aesthetics.
3. Packaging
Packaging products like containers, bottles, and trays are also manufactured through this technique, ensuring high-quality presentation.
4. Medical Devices
The precision of injection moulding is paramount in the medical field, where parts must meet strict regulatory standards and function reliably.
Sustainability in Plastic Injection Moulding
As businesses face growing pressure to operate sustainably, many plastic injection mould makers, including Hanking Mould, are embracing environmentally friendly practices. Here are some strategies being implemented:
- Recycling: Using recycled plastic materials in the injection moulding process.
- Energy Efficiency: Implementing energy-efficient machines and processes to reduce carbon footprints.
- Biodegradable Plastics: Developing moulds for biodegradable materials that break down more easily in the environment.
Choosing the Right Plastic Injection Mould Manufacturer: Key Considerations
When looking for a reliable plastic injection mould manufacturer, consider these vital factors:
- Experience: Look for a company with a proven track record in mould making and a portfolio of successful projects.
- Technological Capability: Ensure the manufacturer employs state-of-the-art technology and machinery for optimal production quality.
- Client Testimonials: Examine feedback from past clients to gauge satisfaction and the reliability of their services.
- Certifications: Check for industry certifications and compliance with quality standards.
Conclusion: The Future of Plastic Injection Moulding
The future of plastic injection moulding looks promising, driven by innovation and demand for quality. As industries continue to evolve, manufacturers like Hanking Mould are committed to meeting these challenges head-on, ensuring that they remain at the forefront of technological advancements. With a focus on quality, sustainability, and efficiency, the plastic injection mould making sector will undoubtedly adapt and thrive in the years to come.
By integrating advanced manufacturing techniques and prioritizing customer satisfaction, plastic injection mould makers will continue to play an essential role in shaping modern production processes across various industries. As a business that stands out in this competitive environment, Hanking Mould is dedicated to providing unparalleled services and products that redefine excellence in the mould-making industry.