The Ultimate Guide to Titanium Bolts Factory: High-Quality Manufacturing and Applications
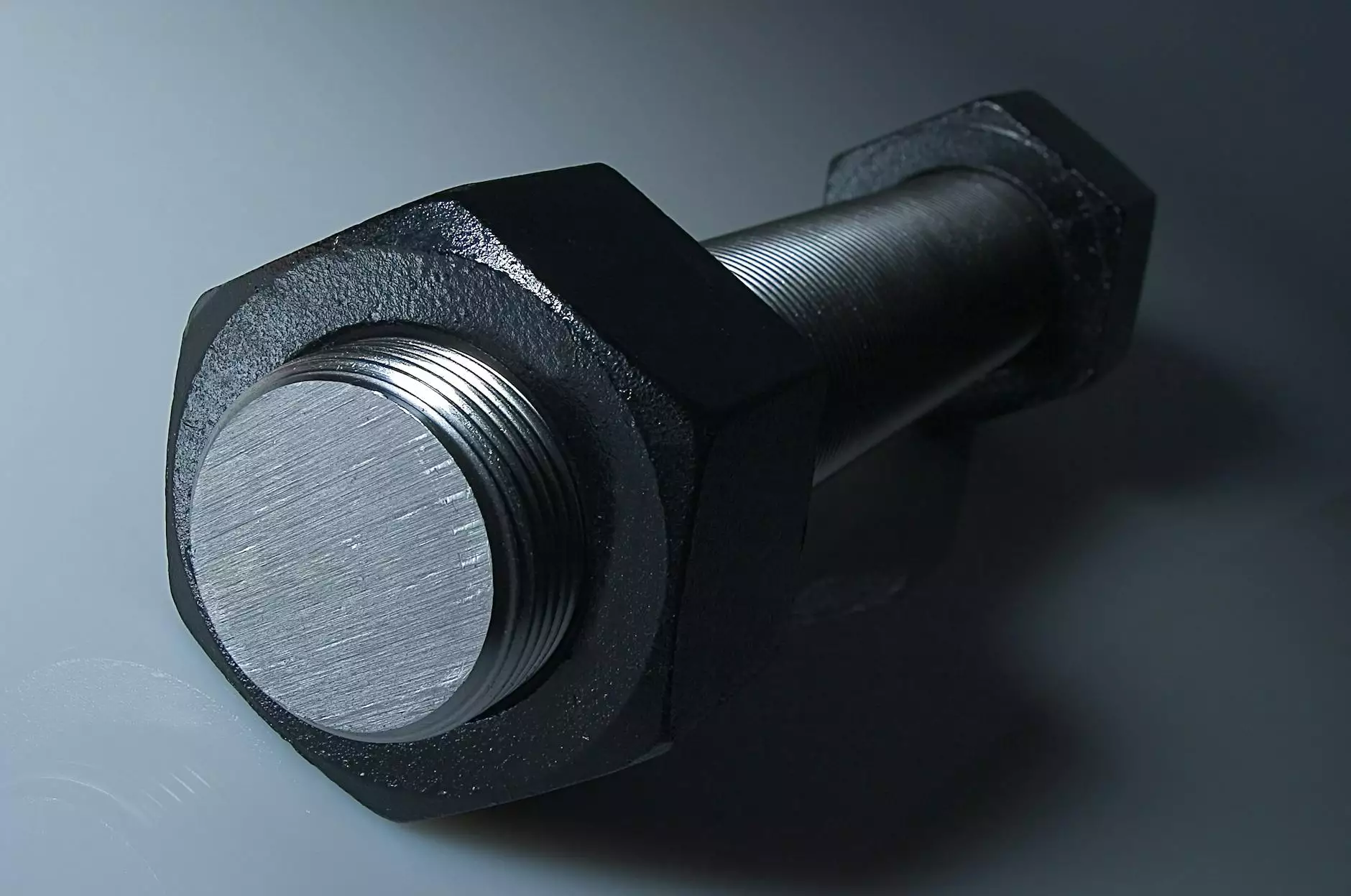
In today's rapidly evolving industrial landscape, the demand for high-performance materials has never been greater. One such material that stands out is titanium, particularly in the form of titanium bolts produced in specialized facilities known as titanium bolts factories. This article dives deep into the fascinating world of titanium fasteners, elucidating their manufacturing processes, unparalleled advantages, and diverse applications across various sectors.
What Makes Titanium Unique?
Titanium is a remarkable metal known for its strength, lightweight nature, and exceptional resistance to corrosion. These attributes make it an ideal choice for demanding applications. To better understand the value of titanium bolts, let's examine the properties of titanium:
- High Strength-to-Weight Ratio: Titanium is as strong as steel yet far less heavy. This key property is beneficial in sectors where weight reduction is crucial.
- Corrosion Resistance: Unlike many metals, titanium forms a protective oxide layer which prevents rust and degradation, making it suitable for marine and chemical applications.
- Biocompatibility: With its non-reactive nature, titanium is often used in medical implants and devices.
- Temperature Resistance: Titanium maintains its integrity at high temperatures, making it useful in aerospace and automotive industries.
The Manufacturing Process at a Titanium Bolts Factory
The production of titanium bolts involves several intricate steps that highlight the metal's unique properties. Understanding this process is essential for recognizing the quality of fasteners produced. Here’s a typical workflow in a titanium bolts factory:
1. Sourcing Raw Materials
The first step involves procuring high-purity titanium ore, usually in the form of rutile or ilmenite. The quality of titanium sourced directly impacts the performance of the final products.
2. Melting Process
Once the raw material is sourced, it undergoes melting in a vacuum environment to prevent contamination. This melting usually occurs in an electron beam or arc furnace, ensuring maximum refinement.
3. Alloying
For many applications, pure titanium is alloyed with other elements such as aluminum or vanadium to enhance specific properties. This step is vital for achieving desired mechanical characteristics.
4. Forming and Shaping
After melting, the titanium alloy is formed into various shapes, including bars and plates, through processes like forging or rolling. These forms are then crafted into bolts using machining techniques.
5. Precision Machining
This step includes cutting, threading, and polishing. High precision is critical here, as even minor deviations can affect the performance of the bolts in application.
6. Quality Control
Each batch of titanium bolts undergoes rigorous testing, including tensile tests and corrosion resistance assessments to ensure they meet industry standards. A dedicated quality assurance team oversees this critical phase.
7. Surface Treatment
To enhance performance, surface treatments may be applied. Common options include anodizing and coating, which increase corrosion resistance and provide aesthetic finishes.
Benefits of Using Titanium Bolts
The advantages of titanium bolts, produced in specialized factories like titaniumbolts.com, are numerous:
- Durability: Thanks to their corrosion-resistant properties, titanium bolts last longer and require less frequent replacements.
- Lightweight: The significant reduction in weight can lead to cost savings in structural support and transportation across various industries.
- Longevity: The lifespan of titanium bolts often surpasses that of steel or aluminum alternatives, making them a smart long-term investment.
- Lower Maintenance: Reduced risk of rust and other forms of wear results in lower maintenance costs over time.
Applications of Titanium Bolts
The versatility of titanium bolts allows them to find applications in a wide array of industries:
Aerospace Industry
Lightweight yet strong, titanium bolts are pivotal in aircraft manufacturing. They contribute to fuel efficiency and overall performance by reducing aircraft weight.
Automotive Sector
The demand for fuel-efficient and high-performance vehicles has led to the increased use of titanium bolts in automotive applications, particularly in racing and high-end performance cars.
Medical Applications
Due to their biocompatibility, titanium bolts are often used in surgical implants, dental applications, and prosthetics, offering longevity and resistance to bodily fluids.
Marine and Chemical Industries
Titanium's resistance to saltwater corrosion makes it ideal for marine engineering, while its inertness makes it suitable for use in chemical processing equipment.
Choosing the Right Titanium Bolts Factory
When considering the purchase of titanium bolts, selecting the right manufacturer is imperative to ensure quality and reliability. Here are key factors to evaluate:
- Quality Assurance Programs: Look for companies that adhere to strict quality standards and have a comprehensive testing process.
- Manufacturing Experience: A factory with a long-standing history in manufacturing titanium fasteners will likely have more refined processes and better output quality.
- Customized Solutions: Some applications may require specialized bolts; ensure the factory offers customization options to meet specific needs.
- Certifications: Opt for manufacturers that have obtained relevant industry certifications, ensuring they comply with safety and quality regulations.
Future Trends in Titanium Fasteners
The market for titanium fasteners is poised for growth as industries evolve. Future trends may include:
- Additive Manufacturing: Innovations in 3D printing technology could enable more complex geometries and lightweight designs, revolutionizing titanium bolt manufacturing.
- Increased Demand in Renewable Energy: As the world shifts towards renewable energy sources, the demand for durable components in wind turbines and other clean energy technologies will likely drive growth in titanium fasteners.
- Sustainability Practices: The emphasis on eco-friendly manufacturing processes may prompt titanium factories to adopt more sustainable practices, further enhancing their market appeal.
Conclusion: The Indispensable Role of Titanium Bolts
In summary, the titanium bolts factory stands as a beacon of innovation in modern manufacturing. The unique properties of titanium, coupled with the advanced manufacturing techniques employed in dedicated factories, yield unparalleled fasteners that serve crucial roles in various industries. With ongoing advancements and a growing market, the future of titanium fasteners looks bright, underscoring their essential contribution to engineering and technological progress.
To explore high-quality titanium bolts tailored to your specific needs, visit titaniumbolts.com and discover a world of exceptional manufacturing excellence.